Losing a bag at the airport is a universal experience. You hop off your flight, make a mad dash to baggage claim, and patiently wait as the same people that you flew in with slowly inch closer to the carousel, leaving you no room to grab your bag. The only issue, however, is that there is no bag to grab. It’s gone.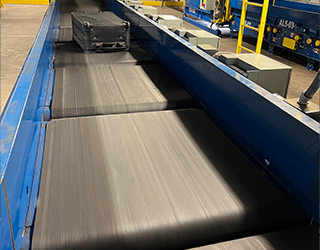
When the everyday traveler runs into this situation, they may ask themselves “how did this happen again?!” But, when you’re part of the ever-evolving airport logistics industry, you can probably give some guidance into which part caused a problem somewhere along the way: the conveyor system.
Losing a bag is only one part of the problem, though. Airports and airlines alike face a litany of challenges when dealing with their conveyor systems, leading to a negatively impacted baggage handling processes and an increasingly frustrated customer base.
We Have a Problem
From ‘simple’ jams to passenger error, airports are hotbeds of opportunity for potential baggage handling issues. And with the peak season of Memorial Day to Labor Day on the docket, issues will only compound here on out. What are some of the main baggage handling challenges that airports face?
Increased Bag Traffic
It’s no secret that warm weather brings more travelers. When you look at the numbers, though, is when you see how much of an impact that it can truly have. In the past twenty years, the months of May through August have boasted an approximate increase of 13.1% travelers over other months.
That means there are an average of over 8.5 million more passengers, and therefore potential incident opportunities, per month during peak season.
Broken, Mistracked, and Lost Bags
When baggage handling systems are not operating at peak efficiency, bags and packages are at a heightened risk of being broken, mistracked or lost in the system.
As a result, passengers can end up having to spend a sizable portion of their travel time attempting to locate their bag, losing their bag all together, or can even end up having to replace their bag on the fly due to irreparable tears, rips, and cracks to their luggage.
Baggage Jams
Depending on a multitude of factors, from bag type to conveyor transfer specs, a passenger's bags can become stuck in the baggage handling system. During the transfer from belt to belt, luggage has a seemingly small window of an opportunity to become stuck, but that small window is all they need.
This can lead to significant delays in multiple ways. First, workers may need to manually remove bags which can take some time depending on their current tasks. Additionally, jammed baggage can pile up, leading to bottlenecks and delays throughout the baggage handling process.
Bag Hygiene
An often-overseen challenge for the airline industry is bag hygiene. In short, loose straps and tags from passenger bags can become caught and cause a massive buildup of luggage at the EDS machines.
Unfortunately, this issue is only going to continue to rise as Self Bag Drop is becoming adopted at major global airports, allowing passengers to process their own bags and introduce them directly into the BHS system. But who is inspecting the bags for hygiene issues like lose straps, handles, or bags that already have damage? A hurried passenger who is running late for their flight.
Why are these an issue?
Ultimately, the aforementioned baggage handling issues can and will hurt your bottom line. But why is it important to take swift and immediate action to resolve them?
Worker Safety
Workers that are handling baggage in outdated and inefficient systems are generally more susceptible to unsafe working conditions. The gaps between conveyor belts present opportunities for a worker to hurt themselves, especially when dislodging a piece of luggage.
Furthermore, luggage buildup from poorly run baggage handling systems cause jams and bottlenecks that can lead to bags falling and potentially injuring your workers. In addition to being a high financial burden, an unforeseen injury depletes your already hard-pressed workforce.
Costly Replacements and Repairs
Broken and lost bags do not only cause massive headaches for individual travelers, but the airline industry can also feel the pain in their wallet. In fact, the industry as a whole can end up having to pay upwards of $2.5 billion, just as they did in the calendar year for 2019.
Additionally, baggage jams that occur at conveyor transfers can cause issues with the entire conveyor belt system, like belt damage, splice damage, and mistracking. The need to resolve these issues leads to further delays and repairs that cost you serious time and money.
Customer Satisfaction
When a missing or damaged bag causes a severe drop in your customer's travel experience, you are setting yourself up to lose them. This sentiment is especially important to the airline industry as customers can just as easily choose the loyalty program of a competitor.
In 2020 alone, Delta Air Lines’ Sky Miles loyalty program had a nearly $26 billion valuation, showing that there is tangible value in ensuring your customer base is treated right. Their needs should not only be met at 35,000 feet, but on the ground as well.
So, what is the solution?
In recent years, the team at Flexco has been developing a specific solution that aims to negate the common issues that baggage handling systems present. As an Industry Manager for Flexco, I am proud that I can offer my aviation industry contacts such a comprehensive solution: the Segmented Transfer Plate.
How do Segmented Transfer Plates work?
After extended research and trials, we found that the best way to mitigate common issues was to address the gaps in the conveyor belt transfer points. Our Segmented Transfer Plates tightly mount to the conveyor belt structure, providing a smooth transition between belts.
Once installed, they effectively block gaps between conveyor belt transfer points, reducing the possibility of baggage jams and lost or broken bags in your baggage handling system. In turn, more bags are delivered in a timely manner, and you will have a higher likelihood of satisfying your customer base.
Best of all, Segmented Transfer Plates are a simple-to-use solution that keeps the quick turnaround needs of our customers in mind. The average installation time is now averaging out to around 20 minutes, meaning your workforce can get back to more important tasks quickly and efficiently.
Real World Performance
Additionally, I would like to invite you to take a look at a recent Application Profile we created on one of our Segmented Transfer plates in-action during the X-ray conveyor/baggage inspection stage of the process. The Application Profile goes into detail on one airport’s specific baggage handling problem and how Flexco technology provided positive results.
View Here
Prepare for Takeoff
Although the solution seems simple, I firmly believe that once you adopt Flexco’s Segment Transfer Plates into your baggage handling system, you will see just how revolutionary it is as it saves you time, money, and the headache of an outdated system.
So, what is the next step? I recommend a live product demo. In doing so, product experts from Flexco will visit your facilities and determine the best solution for your specific transfer points.
After implementing our demo Segmented Transfer Plates, we would like you to see just how much of an effect they have on your real-world processes. After that, we begin discussion on the best way to integrate our technology into the rest of your baggage handling system.
Request Demo
Authored by: Todd Stewart, Industry Manager
Stewart focuses on both the logistics industry, creating programs to support each segment and identifying customer issues, as well as potential product solutions, for parcel, airports, warehousing, distribution, and fulfillment. Stewart began his career at Flexco in 1989, working in various roles from customer service, to manufacturing, to training, to new product development, to market development management before taking on the role of Industry Manager in 2017. He earned a bachelor’s degree in Marketing with a B2B specialty from Davenport University.