Conveyor belt vulcanization and mechanical fasteners have both been popular for quite some time. Using heat and pressure to create a strong chemical bond is appealing for some, while others prefer the convenience of mechanical fasteners.
For heavy-duty industries, the debate on which splicing method is best is still ongoing. In fact, choosing between mechanical fastening and vulcanizing has been a conversation that Flexco has been leading for many years.
Many factors come into play when deciding between conveyor belt fasteners and vulcanization. The determination between the two depends on the belt, application, environment, production goals, and budget.
Before you get into the weeds on what works best for you, let's take a look at some of these factors in more detail.
The Challenges of Belt Vulcanization
A huge benefit to my job is that I am in the field for a decent portion of my schedule. While on site, I get to hear firsthand from managers and technicians on what is working for them, and what is causing production problems.
Many of these conversations have started during mechanical belt fastener installations, eventually turning into a discussion comparing the two methods. During a recent visit, I asked the site manager how they decided between the two for this particular belt. Their response highlighted two interesting points.
1. There Is a Product Knowledge Gap
Belt vulcanization can be incredibly difficult. Often, sites lack staff with dedicated equipment and expertise to install a vulcanized splice, so they need to use a third party.
Using a contracted service for vulcanization is not necessarily a bad thing. Specialized crews are usually incredibly knowledgeable, and if you use a reputable distributor, it can pay dividends. However, some may find that scheduling and availability is a real barrier.
Installation of Flexco fasteners is much simpler. Our installation tools are engineered to enable first-time users to perform like experts. Maintenance teams can even utilize common tools that they probably already have on site. This effectively limits the likelihood of installation failure, as workers are more confident in their performance from the start.
2. Downtime + Availability + Cost = A Big Investment
By far the largest deterrent to adopting vulcanized belt splicing is that it can be expensive. Whether it is the initial investment or the prolonged downtime, the process is costly.
Extended downtime becomes much less of an issue when using mechanical belt fasteners. Because they are inexpensive and readily available, on-site teams can make downtime repairs a less time-consuming process. This is especially crucial as vulcanization can take 24 hours or more when factoring in scheduling.
In short, fasteners can perform similarly to vulcanization at a fraction of the price. The question that site managers must ask is whether the investment and time commitment is worth it when a cost-effective and efficient solution like fastening is readily available.
How to Choose the Right Fastener
Flexco has been in business for over 100 years, and in that time, we have always made top of line mechanical belt fastening systems. From Alligator® and Clipper® to XP™, Flexco has become a staple name (no pun intended) for belt conveying.
Although there is no one-size-fits-all approach for choosing mechanical belt fasteners, we do have some general rules that you can follow.
Fastener Type Selection
If you are not quite sure which fastener meets your specifications, use our Heavy Duty Mechanical Belt Fastener Selection Calculator. By entering your information on belt tension and thickness, and minimum pulley diameter, we can better estimate your needs.
For an even more comprehensive breakdown, be sure to utilize our product overview.
Fastener Material Selection
Getting long-term results from belt fasteners is highly dependent on choosing the right material for your application. To meet the needs of many different heavy-duty work environments, Flexco has developed a specialized catalog.
Whether the material you work with is highly flammable, susceptible to magnetics, or anything in between, Flexco has the right option for you. Reference the chart above or ask our customer service team for more information on what is best for you.
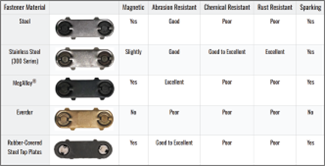
The Final Verdict
Overall, both vulcanization and fastening are great options depending on the situation.
Mechanical belt fasteners offer users a strong and easy-to-use platform for conveyor systems at an affordable price, while vulcanized conveyor belts offer users a comprehensive integrated splicing solution.
If you would like on-site support selecting the solution best-suited for your application, I would advise you to reach out to Flexco for a full conveyor assessment and site walkthrough. While at your facility, our field specialists diagnose your needs and provide you with insight specific to your process.
We also offer Heavy-Duty Mechanical Belt Fastener Training Schools multiple times a year where our experts will walk you through selection, installation, troubleshooting, and answer questions to help you maximize your productivity. Have a Flexco expert out to your site to train your team today!
Authored by: Franklin Moore, Product Manager