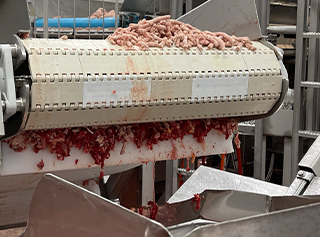 |
Ground beef carries back over the belt, sticking to the belt and falling to the floor. |
You may have heard the old saying, “Time is money.” If only time was the one thing that cost us money. In the proteins industry, there are a lot of things that cost us money that we can never get back. An employee calling in sick, a piece of equipment going down for a period of time while it is waiting to be fixed, and a missed customer deadline are just a few of the things that come to mind. And oh, what about the perfectly good product that falls off the belt onto the floor (rendering it to scrap), decreasing your yield and also keeping your maintenance team busy cleaning up?
Product Waste Is Money.
You may have never thought about it that way because the problem has always been there and you’ve kind of ignored it, but it’s true. Every pound of beef, or chicken, or pork you are scooping up off the floor is costing you in two ways: Yield and Maintenance Time. The good news is … it doesn’t have to be like that forever. There is a simple solution to eliminating product waste under your conveyors. But in order to understand the solution and how it works, let’s start with the cause of that waste.
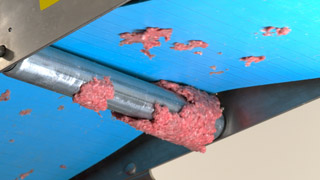 |
Ground beef carryback that is sticking to the underside of the belt and roller. |
What is belt conveyor carryback?
Product that sticks to the conveyor belt and either falls onto the floor or continues on the belt and adheres to other conveyor components is commonly called “carryback.” And the reason carryback is happening is because proteins are inherently sticky and if there is nothing to scrape the belt as the product is transferred from one conveyor process to another, it will either find the floor or gunk up your conveyor and associated components.
Oftentimes, you will see that an OEM has thought of this fact and installed a piece of UHMW to scrape the belt as part of its design. The problem is that the UHMW is usually bolted to the structure, which is then bolted to the conveyor, and there is no way to clean it quickly and regularly without unbolting it (which could be a sanitation nightmare). The other problem is that the UHMW wears over time and loses contact with the belt, making it unable to scrape it anymore.
For this reason, we suggest the use of an engineered belt cleaner. An engineered belt cleaner works just like you would think. It is specifically engineered to clean a belt, not an afterthought to an overall conveyor design. And an engineered belt cleaner is more than just a bolted on piece of plastic, belting, or rubber – it is mounted to the structure and contains tensioners to keep constant blade-to-belt contact. Engineered cleaners made from food-grade materials are specially designed to work in facilities that process foods, like proteins, with easy assembly and disassembly for cleaning and sanitization.
A $713,000/year waste problem in protein processing
For a pork producer in Middle America, a “Waste Walk” through their facility discovered that the product that was falling off their belts accounted for more than just a few pounds a day. When measured, the operation was losing more than 3,100 lb. of material from their ham trim line alone. The homemade belt scraper they were using would work well at first, but would then begin to fail over time as blade wear was not allowing the static-mounted blade to stay in contact with the belt. This also meant the maintenance team was busy keeping the floor free of slip-fall hazards instead of proactively focusing on maintaining other important areas of the operation.
What is a Waste Walk? |
A waste walk is a visual sweep of the plant that can identify areas of product waste. Anything laying on the floor or stuck in your conveyor frame and components can be considered a waste because it left the conveyor and never got to its intended location. This means a lot of expensive product never reached the customer. Once problem areas are identified during the walk, a plan is made to address and eliminate waste. |
A visit from the local distributor yielded a possible cleaning solution that the plant was eager to try on their plastic modular belting. The USDA-certified FGP Food Grade Precleaner from Flexco seemed like the right fit for the job because of its easy-to-adjust spring tensioning unit, which ensures constant blade-to-belt contact. Plus, assembly and disassembly for cleaning and blade changes only involve snapping blades on and off the unit, making it a time-saver for the sanitation team.
Once the FGP Food Grade Precleaner was installed, results were immediate, with little to no carryback on the inclined conveyor. Through the use of the FGP, wasted product was reduced by more than 3,100 lb. a day, for an overall savings of $713,000 a year.
Additionally, the several trips needed per day to manually empty a bin kept under the conveyor were reduced because scrap decreased by approximately 90 percent. This saved the maintenance team time and also decreased the potential danger of working near a running conveyor. An added benefit to the addition of the FGP Food Grade Precleaner was that the floor was clear of trimmed pork, creating a safer environment for those walking through the plant.
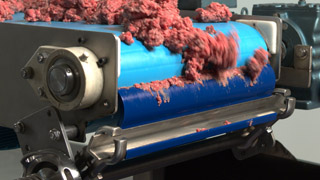 |
Flexco FGS Food Grade Secondary Cleaner preventing ground beef carryback and product waste. |
Is an engineered cleaner the right choice for your belt conveyor?
When it comes to product waste, the right cleaner can make all the difference for your operation. Since the launch of the FGP Food Grade Precleaner, Flexco introduced the FGS Food Grade Secondary Cleaner. The FGS Food Grade Secondary Cleaner is easy-to-install and features solid, stainless steel components to make it easy to maintain. We’ve also made cleaning and sanitation a snap with quick and easy disassembly in less than a minute, with limited components and no need to remove the cleaner from the structure.
Not sure if an engineered cleaner is worth the time and money?
They will help you identify your most troubled conveyors, help you understand the costs of the waste, and offer solutions to reduce your product waste.
Authored by: Jonathan Morgan, Industry Manager – Food Processing
As an Industry Manager at Flexco, Morgan focuses on the food processing industries, including proteins, baking, and produce. Morgan has a mechanical engineering education, application knowledge, extensive industry network, and technical sales support experience.