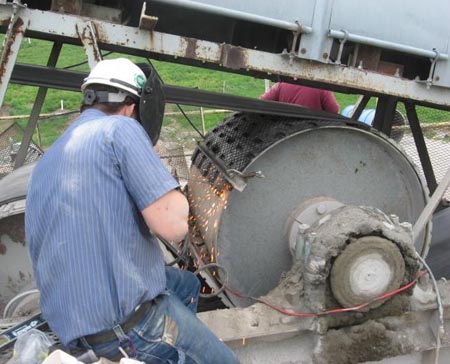
Industry
Aggregates
Application
Midwestern aggregates operation
Product
Flex-Lag® Weld-On™ Rubber Pulley Lagging
Objective
A lagging solution for better cleaner compatibility
Conveyor Detail
3 ply x 330 belt
Lagging installed on head pulley
Precleaner on head pulley
Problem
The lagging system of a Midwestern aggregates operation was comprised of strips that slid into place and were then welded on either end to secure. After installation, large gaps were evident between the strips, causing the cleaner blade to drop into the gaps. Without consistent blade-to-belt contact, the blade was quickly wearing down and causing a chatter noise, resulting in unnecessary costs for purchase and installation of replacements.
Solution
The company needed to find a lagging solution that would be compatible with its precleaner. With its patented gear tooth design and ease of installation, Flex-Lag® Weld-On™ Rubber Pulley Lagging offered an effective solution. Unlike their existing lagging, this weld-on rubber lagging was manufactured to fit right onto the pulley without having to be cut to fit. In addition, by installing Flex-Lag Weld-On Rubber Pulley Lagging, the wide gaps between strips were eliminated.
Result
Flex-Lag Weld-On Rubber Pulley Lagging has made a big difference at this facility by decreasing issues with cleaner compatibility. Since the installation, the precleaner blades have not seen wear or needed replacement. Maintenance downtimes for retensioning and blade replacements have significantly diminished. With the average cost of downtime at an aggregates operation costing $1000 an hour, this savings is crucial. The blade runs smoothly along the head pulley and the loud chattering noise has been completely eliminated with the newly installed lagging. Based on the success of his current lagging installation, the customer stated that he is definitely considering replacing his other slide-type lagging with the weld-on rubber lagging.