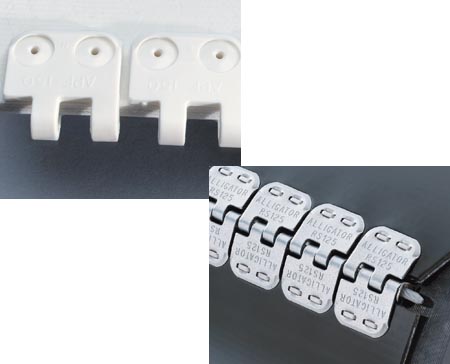
Industry
Food processing
Application
Fish processing
Product
Alligator® Plastic Rivet and
Alligator® Staple Fasteners
Objective
Reduce time spent cleaning belt conveyors, meet FDA requirements
Conveyor Detail
24" wide polyurethane, tabletop belts
Problem:
The crew at a tuna processing plant located in Ecuador was spending seven to eight hours a night sanitizing their belts in an attempt to comply with FDA rules. The topsides of the vulcanized belts were easy to clean, but crews had a difficult time cleaning under the belt. Water and fish particles would attach to the underside of the belt, causing the plant to smell and corroding the first ply of the belt carcass. After five or six months, belts were breaking and the plant was not passing inspection. The FDA found large amounts of contamination during testing and gave the plant a timeframe in which to fix the cleaning processes.
Solution:
After consulting with the local distributor, the plant superintendent decided to try Alligator® fasteners instead of endless splicing the belts. With hinged fasteners, the maintenance crew could simply take out the hinge pin and pull the belts apart to sanitize both the top and bottom of the belt. This could not be done with the endless belts, making them extremely difficult to clean. Alligator Plastic Rivet fasteners were used on the belts that came into direct contact with the tuna, while Alligator Ready-Set™ Staple fasteners were used on belts that carried trays and waste disposal belts.
Result:
The crew simply removes the pins, pressure-washes the top and bottom of the belts, and dips them into three containers of chemicals for sanitation purposes. The cleaning manpower was cut in half, and the actual time spent cleaning was also reduced by 50 percent. Since the plant did not have to close early for cleaning, it gained three additional hours of production per day. Belts that used to fail after only five or six months are now lasting 1 1/2 to 2 years, and production does not need to be shut down for vulcanization if a belt fails. To save even more time, the maintenance crew receives belts with fasteners already attached from the distributor. When it is time to change belts, they simply connect the old belt with the new belt and pull it through the system. The new sanitizing process has since met FDA requirements.