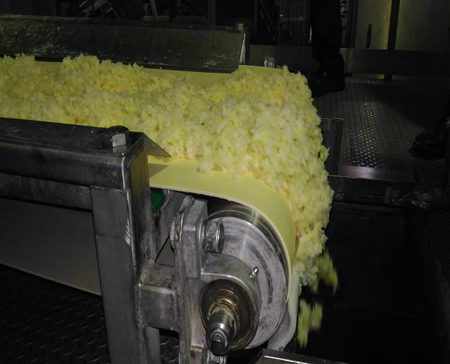
Industry
Food
Application
Mixer reversible belt
Product
FGP Food Grade Precleaner
Objective
Reduce carryback
Eliminate belt mistracking
Reduce product waste
Problem:
A major food operation in India struggled with product scrap, productivity issues, clean up, and most importantly belt mistracking due to material carryback on the mixer reversible belt that was carrying its vegetable products. Carryback occurs when material transported along conveyor belts adheres to the underside of the belt instead of being cleaned off or released. Over the long term, it can lead to even more costly issues, such as product contamination or sizable fines resulting from regulatory noncompliance. Like many other food manufacturers, the maintenance team tried to mitigate the carryback issues with a homemade belt cleaner that consisted of a PTFE blade attached to the conveyor. Unfortunately, it was doing little to solve the carryback problem and the belt was constantly mistracking – needing to be shut down at least once per shift to be realigned.
Solution:
The maintenance supervisor decided it was time to look for a more professional solution. Upon seeing a demonstration of the FGP Food Grade Precleaner from Flexco, he felt it would be a good fit for his conveyor. He was impressed with the fact that the FGP had a spring tensioner, which ensures optimal blade-to-belt tension because of its ability to maintain constant contact with the belt. Many homemade cleaners do not apply enough pressure to the belt to remove all excess product, instead allowing it to accumulate on the belt and conveyor components. Other homemade scrapers apply too much pressure and cause damage to the belt or splice.
Result:
The FGP Food Grade Precleaner significantly reduced the amount of carryback on the system, and the supervisor is pleased with its performance. The plant no longer has excess amounts of materials on the floor, which improves safety and sanitation levels. Increased sanitation was an unexpected benefit for the operation, as the maintenance team learned it can simply snap the blade off and back into place without removing any other parts, reducing the time it takes to clean or replace the blade. The FGP is also designed with stand-offs that allow cleaning without the need to remove the end plates. The instances of carryback building up on conveyor components and ultimately causing belt mistracking were also reduced. Instead of stopping the belts once per shift, they now adjust once every three shifts, which translates to a 60% improvement in uptime. Productivity was also increased by at least 7%, making the cleaner a smart financial investment as it was paid off in the first week of production. For this facility, deciding to go with an engineered belt cleaner has made a big difference in safety, sanitation, and productivity – something a homemade solution just couldn’t deliver.