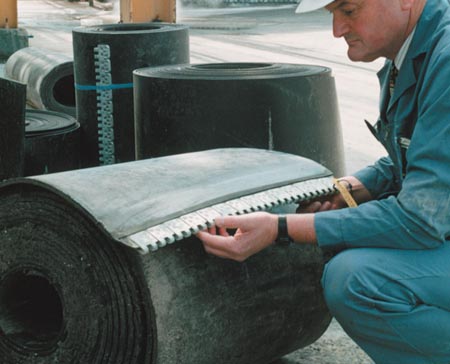
Industry
Agriculture/Hay Baling
Application
Process-stream bulk conveyors
Product
Flexco® SR™ Rivet Hinged Fasteners
Objective
Minimize frequency, downtime and cost of vulcanized conveyor-belt resplicing
Conveyor Detail
Belting: three-ply heat-resistant rubber, 32-40"(812-1016 mm) wide, .37" (9.5 mm) thick
Belt Lengths: 20 “problem” belts, ranging from 10' to 197' (3-60 m) long between end pulley centers, deployed across three production lines
Configuration: primarily horizontal (some slightly inclined), most troughed at 35-degrees, with relatively low operating tension of 86-114 P.I.W. (15-20 kN/m)
Typical Load: up to 200 tpm of NPK fertilizer granules and fines, received from a rotary dryer at up to 212º F (100 º C)
Typical Speed: up to 3.3' (1 m) /sec.
Problem
Hot loads, high cycling due to short distances between pulleys, and the severe flexing around small pulley diameters caused vulcanized splices to deteriorate quickly. Frequently idled production lines piled up intolerable losses for an operation designed to run around the clock all year long. Every time a splice came apart, that line would lose 12 hours of production while a vulcanizing contractor rejoined the belt. On just one belt, where splices rarely lasted more than three months, the cost of lost production, vulcanizing services, and new belting typically required with each splice, was adding up to about $35,000 per year.
Solution
The high temperature “problem” belts were re-spliced with Flexco® SR™ Rivet-Hinged Fasteners, a hinged-plate design consisting of 1-1/2" (38 mm) -wide top and bottom plates joined at one end by two wide hinge loops. Each pair of plates sandwiches the belt end and is secured to the belt with a staggered pattern of five hammer-driven, self-setting rivets. Segments are supplied in strips that assure proper alignment and spacing across the belt end. To avoid possible snagging on scrapers, the fasteners were countersunk flush with the belt’s top cover using a Flexco skiver. Sifting was prevented by plugging the hinge area with a resilient silicone-rubber sealant. Using the smallest of three SR sizes, designated R5, the hinged splices avoided any problem with the plant’s small pulleys.
Result
On the plant’s worst-case conveyor, SR lasted two times longer than previous vulcanized splices ... and on other problem belts, up to five times longer. With such extended life, splices are generally installed only when replacing worn out belts, not because of splice failure. To minimize downtime, the plant stocks a spare for all 20 belts, cut to length and with SR fasteners pre-installed on both belt ends. Plant workers can quickly string the belt through the conveyor, join the ends with a hinge pin, and inject the sealant with a caulking gun, meaning no more waiting for vulcanizers to arrive or for splices to cure. By minimizing downtime production losses, as well as resplicing costs across the system, SR continues to help this plant realize a six-figure savings
every year.
Shop Flexco Fasteners