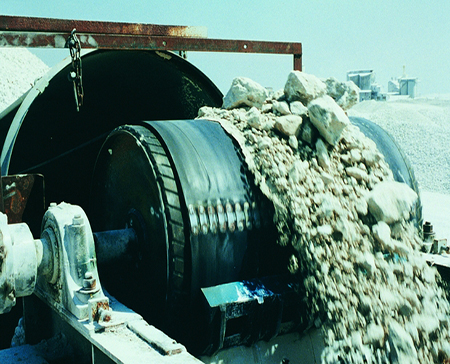
Industry
Crushed limestone aggregate for concrete paving and construction
Application
Processing and stacking conveyors
Product
Flexco® Bolt Solid Plate Fasteners
Objective
Minimize splice wear-out and replacement on wet belts
Conveyor Details
Belting: 2- to 4-ply rubber constructions from 5/16” to 3/4” (8 to 19mm) thick with mechanical fastener ratings around 330 PIW (57.7 kN/m), in widths from 24” to 54” (610 to 1372 mm) Belt Lengths: (between end-pulley centers): 82 belts ranging from 18’ (5.5 m) to 3150’ (960 m) Configuration: horizontal to varying degrees of incline, up to 17º on pit-exit and stacker belts, most troughed at 35º Belt Speeds: 320 to 550 fpm (98 to 168 mpm).
Problem
Known for supplying premium, clean product, this plant passes all material coming up from the pit through rotating-drum scrubbers before stacking on the primary surge pile. From that point forward, loads are typically wet to the point of being a slurry, first passing through washing screens, then through logwashers, finally through final rewash screens before stockpiling. Replacing the bolted-plate belt splicing on wet belts, routinely needed about three times a year, tended to be the plant’s biggest maintenance problem.
Solution
Flexco’s Bolt Solid Plate Belt Fasteners, used throughout the plant, were upgraded from standard mild steel to MegAlloy® on all belts carrying wet product. This proprietary alloy, finished by heat-treating to maximize hardness against wear, is one of half a dozen special metals available with Flexco’s bolt- or rivet-attached heavy-duty fasteners to help them work better in hostile environments. MegAlloy was specially designed as a much less costly abrasion-resistant alternative to stainless steel splicing, which is priced more than six times higher than standard mild steel fasteners.
Result
In highest-wear areas, where fasteners had been replaced three times a year, MegAlloy plates are lasting at least a full year. Although they cost about 85% more than standard steel plates, they ended up saving about 38% of what three sets of standard plates would have cost over the same period. That savings was increased by the maintenance time avoided through the elimination of two replacements per splice during that year period, each estimated to cost $240 to $360 in labor. Less-frequent splice replacement also improved plant productivity by reducing the two-to-three-hour shutdowns needed every time a key belt is respliced.